0 %
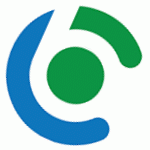
When coating any substrate, the first step is to assess the condition of the surface to have the correct profile and be free of contaminants.
The first criteria typically specified is the cleanliness of the surface. Before any work is carried out on the substrate, the condition of the surface is assessed using a visual comparator of the four rust grades outlined in ISO 8501-1 (A, B, C, D). Removing the mill scale or rust defined by the ISO 8501-1 will require the substrate to be cleaned using grinding or abrasive blasting.
Surface defects should be removed according to the three preparation grades described in ISO 8501-3 before starting any further preparation related to coating.
Please download our guide for preparation grades of welds, edges and other areas with surface imperfections:
Before the surface is blast cleaned, surface contaminants such as salts, oil, grease, cutting oils and drilling compounds should be removed. When applying a second or third coat, the surface could be contaminated with further dust, salt, hot work debris and amine blush. This can be tested using amine blush kits. It would be wrong to assume that the blasting process will remove all these contaminants, what may happen is that whilst they appear to have gone, they will have been distributed over the steel surface as a thin layer.
Surface cleanliness can be split into five categories:
• Visible Contaminants: oil, grease, cutting oils, drilling compounds, etc.
• Dust: blast media, soil, air particulates, etc.
• Salts: all salts and in particular chloride, sulphate and nitrate ions.
• Carbamates: specifically amine blush
• pH
Surface cleanliness tests should be done according to ISO 8502.
ISO 8502-6 and ISO 8502-9 describes the Bresle Method which is suitable for use in the field to determine the presence of soluble contaminants on a surface
Cleaning the surface with a wire brush or scraper can remove small amounts of coating or corrosion but is not very effective in removing mill scale or rust. Power tools are more effective and faster than hand tools. In both cases, however, the profile created in the substrate is minimal.
One of the more common failures of protective coatings is due to inadequate surface preparation of the fasteners, nuts, bolts and screws etc. It can also be caused by the mixing of materials which may lead to bi-metallic corrosion. Structures are carefully designed to avoid dissimilar metals causing this.
The same care and attention in surface preparation should be taken with the fasteners as is taken with the flat/open areas of the substrate. It is often also necessary to use hand tools in these areas.
Abrasive blasting is the most commonly used method for creating the required profile. Generally, abrasive blasting is a method of projecting abrasive media, using compressed air, to remove the coating and/or corrosion from the surface in large blast halls.
Metallic (M) abrasive media according to ISO 11124-1 :
Typical metallic media includes: steel shot, steel grit, stainless steel shot, cut wire, copper slag, aluminium shot and zinc shot. Sometimes a mix of shot and grit is used to create the correct surface.
Non-metallic (N) abrasive media according to ISO 11126-1 :
Olivine, Garnet, Staurolite
Particle size has an important effect on the number of impacts per second of blasting, so it is advisable to use media of the smallest screen size that will do the work. There will be a higher number of smaller particles in a given volume than larger particles, hence more impacts on the surface, reducing process time to a minimum.
Important parameters need to be controlled/monitored during blasting. These include: Pressure, Nozzle Size (diameter), Climatic Conditions, Monitoring Cleanliness of the Water & Blast Media, Testing Chloride Concentration in Abrasives, Testing the Chloride Content in Water.
ISO 8501-1 identifies the appearance using grades of cleanliness together with reference pictures.
There are four grades of cleanliness for abrasive blast cleaning of new steel: Sa 1, Sa 2, Sa 2½ and Sa 3
The specification for the coating will detail which grade of cleanliness is required. To assess the cleaned surface it should be compared to the appropriate photographs in the standard. Beware, these standards are often referred to as profile standards, this is not the case, they are surface cleanliness standards - the two are commonly confused.
For steel, surface profile is a measurement of the peak-to-valley height of the surface. By creating a profile on a substrate, the overall surface area of the substrate increases significantly. The more the profile increases, the greater the increase in surface area. The profile therefore, provides the coating with a greater surface area, leading to increased coating adhesion.
Surface comparators are used to compare freshly blasted profiles to pre-defined profiles according to ISO 8503-1 and ISO 8503-2.
BROCOAT ENGINEERING SURFACE PREPARATION PROJECTS
ISO 8501 - Preparation of steel substrates before application of paints and related products – Visual assessment of surface cleanliness
ISO 8501-1 : Rust grades and preparation grades of uncoated steel substrates and of steel substrates after removal of previous coatings
ISO 8501-2 : Preparation grades of previously coated steel surfaces after localized removal of previous coatings
ISO 8501-3 : Preparation grades of welds, cut edges and other areas with surface imperfection
ISO 8501-4 : Initial surface conditions, preparation grades and flash rust grades in connection with high-pressure water jetting
ISO 8502 - Preparation of steel substrates before application of paints and related products – Tests for assessment of surface cleanliness
ISO 8502-2 : Laboratory determination of chloride on cleaned surfaces
ISO 8502-3 : Assessment of dust on steel surfaces prepared for painting (pressure sensitive tape method)
ISO 8502-4 : Guidance on the estimation of the probability of condensation prior to paint application
ISO 8502-6 : Sampling of soluble impurities on surfaces to be painted – The Bresle method
ISO 8502-9 : Field method for the conductometric determination of water-soluble salts
ISO 8503 - Preparation of steel substrates before application of paints and related products – Surface roughness characteristics of blast-cleaned steel substrates
ISO 8503-1 : Specification and definition for ISO surface profile comparators for the assessment of abrasive blast-cleaned surfaces
ISO 8503-2 : Method for the grading of surface profile of blast-cleaned steel – Comparator procedure
ISO 8503-3 : Method for the calibration of ISO surface profile comparators and for the determination of surface profile – Focusing microscope method
ISO 8503-4 : Method for the calibration of ISO surface profile comparators and for determination of surface profile – Stylus instrument
ISO 8503-5 : Replica tape method for the determination of surface profile
ISO 8504 - Preparation of steel substrates before application of paints and related products – Surface preparation methods
ISO 8504-1 : General principles
ISO 8504-2 : Abrasive blast-cleaning
ISO 8504-3 : Hand and power tool cleaning
ISO 12944 - Paints and varnishes – Corrosion protection of steel structures by protective paint systems
ISO 12944-3 : Design considerations
ISO 12944-4 : Types of surfaces and surface preparation
ISO 11124 - Preparation of steel substrates before application of paints and related products – Specifications for metallic blast-cleaning abrasives
ISO 11125 - Preparation of steel substrates before application of paints and related products – Test methods for metallic blast-cleaning abrasives
ISO 11126 - Preparation of steel substrates before application of paints and related products – Specifications for non-metallic blast-cleaning abrasives
ISO 11127 - Preparation of steel substrates before application of paints and related products – Test methods for non-metallic blast-cleaning abrasives
ASTM D 4940 - Standard test method for conductimetric analysis of water soluble ionic contamination of blast cleaning abrasives