0 %
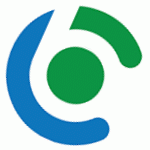
All methods of thermal spraying involve the projection of small molten or softened particles onto a prepared surface where they adhere and form a continuous coating. As the heat energy in the molten particles is small relative to the size of the workpiece, the process imparts very little heat to the substrate. As the temperature increase of the coated part is minimal, heat distortion is not normally experienced, which is also a major advantage over hot-dipped galvanising or welding.
Thermal spraying is a technology which protects and greatly extends the life of a wide variety of structures, equipment, and vessels, in the most hostile environments and in situations where protective surface coatings are vital for longevity. Type of environment, proper surface preparation, thickness of coating, use of sealers and/or topcoat, and the nature of the structure are all important elements when considering a coating system. Each job must be treated individually, as requirements for protection may differ. There are hundreds of case histories relating to the longevity of zinc thermal sprayed coatings on steel. Bridge structures, interiors of potable water tanks, pipelines, and dam locks show, in many cases, over 30 years of service without major repair.
Thermal metal spray requires high attention to personal safety and the thermal spray operator must be specially trained, both for quality and for safety reasons.
BROCOAT ENGINEERING METALLIZATION PROJECTS
ISO 2063 - Thermal Spraying - Zinc, Aluminium And Their Alloys
ISO 2063-1 : Design Considerations And Quality Requirements For Corrosion Protection Systems
ISO 2063-2 : Execution Of Corrosion Protection Systems
ISO 12679 - Thermal Spraying - Recommendations For Thermal Spraying
ISO 14918 - Thermal Spraying - Approval Testing Of Thermal Sprayers