0 %
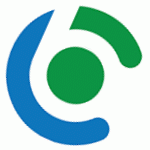
A. Binders
Natural Resins:
• Drying oil, Bitumen, Wood rosin
Synthetic Resins:
• Alkyd, Acrylic (Water borne or Solvent Borne), Epoxy, Polyester, Polyurethane, Silicate, Vinyl ester, Polysiloxane
B. Pigments
• Colouring, Inhibitive Pigment, Cathodic protective, Biocides
C. Extender
• Calcium carbonate/Chalk, Barium sulphate/Baryte, Mica, Talk, Dolomite
D. Solvent
• Hydro carbons, White spirit, Xylene, Ketones, Esters, Glycol ethers, Alcohols, Water, Styrene
E. Additives
• Wetting Agent, Anti-settling, Drier, Anti-skinner, Plasticizer
Binders
Describes the type of paint/coating (generic type) and whether the coating is organic or inorganic. Organic coating is based on a binder that is carbon based e.g. made from oil (EP, PU, PE)
where inorganic coating is based on a binder that is not carbon based, typically silicate (Zinc alkyl silicate, Zinc alkali silicate) and usually pigmented with metallic zinc which is electrically conductive.
Modified Binders
Containing more than one binder (Epoxy Mastic, Vinyl Epoxy) or modified chemically by attaching new molecule groups to their molecules (Styrene modified alkyd, Urethane modified alkyd, Epoxy ester)
Solvent vs. Thinner
Solvent is the raw material used when making paints and thinners and dissolves the binder completely (forms a solution). Thinners are the commercial products that are used to lower the viscosity (and for cleaning the equipment).
Only the thinners named in the TDS should be used in the correct percentage. Excessive thinning and unknown thinners should be avoided in order to have correct application and drying, otherwise desired durability can not be achieved.
The properties of a paint film are closely related to how the binder dries or cures. The four most common drying/curing mechanisms are:
• Physical Drying (solvent evaporation)
• Oxidative Curing (reaction with oxygen in the air)
• Chemical Curing (chemical reaction between base and hardener)
• Coalescence (evaporation of water followed by merging of the paint droplets)
The generic type refers to the ingredient responsible for the basic properties of the paint. In most cases the binder dictates the properties, and defines the generic type.
• Acrylic
• Alkyd
• Epoxy
• Zinc rich epoxy
• Polyester
• Polysiloxane
• Polyurethane
• Silicone
• Inorganic zinc silicate
• Vinyl
• Vinyl ester
Shopprimers
Shopprimer is a quick drying paint applied as a thin film to a metal surface after blast cleaning, to give corrosion protection during the period before and during fabrication.
It must not interfere with the speed or quality of cutting and welding of the steel during fabrication, so DFT must be low. While other paints generally are classified according to their type of binder, shopprimers are often classified according to their main pigment content:
• Iron oxide shopprimers (3-5 months of corrosion protection for 20 µm)
• Zinc rich shopprimers (8-10 months of corrosion protection for 20 µm)
• C1 (Very Low Corrosivity)
• C2 (Low Corrosivity)
• C3 (Medium Corrosivity)
• C4 (High Corrosivity)
• C5 (Very High Corrosivity)
• CX (Extreme Corrosivity)
• Im1 (Immersive Corrosivity - Fresh water)
• Im2 (Immersive Corrosivity - Sea or brackish water)
• Im3 (Immersive Corrosivity - Soil)
• Im4 (Immersive Corrosivity - Sea or brackish water with cathodic protection)
Durability categories and ranges
• L (Low - Up to 7 years)
• M (Medium - 7 to 15 years)
• H (High - 15 to 25 years)
• VH (Very High - More than 25 years)
Corrosion can take place on any part of a steel structure, particularly in places where the corrosion protection is weak or damaged. During spay application of corrosion protective coatings, certain areas and positions may be difficult to reach or access with a spray gun, or the coating may tend to pull away from edges or refrain from entering tiny gaps, such as; profiles, inside edges, holes, notches, corners, angles, sharp edges, pits, manual welding seams, behind flanges
By applying one or two coats by brush before (or after) the spray application takes place, thickness of the protective paint film is increased in those vulnerable areas and thereby danger for corrosion decreases. This is called “stripe coat”, since it predominantly ends up being paint applied in stripes on all the edges, welding seams, angles, etc.
A high quality paint brush is an excellent tool for stripe coating, the brush wets the substrate properly and works the paint well into the substrate. Stripe coating will improve the life time of the paint system. Contrasting colours between the stripe coat and the full coat will make it easier for the painter to see where it has been applied and easier to inspect as well.
Application by Airless Spray
Airless spray application is the preferred method for most construction and maintenance industry. It is quick and cost efficient, can build up a high film thickness in individual coats and usually gives an attractive finish. The force of the airless spray will ensure a good wetting and penetration into the surface profile.
Benefits:
• Very high productivity (Up to 75% compared to other methods)
• Applicability of high viscosity paints
• Higher thickness in a single coat
• Even film thickness
Limitations:
• Safety-high pressures
• Higher loss for smaller sized objects
• Complicated and expensive equipment
• Skilled applicator required
Airless Spray Nozzle Size Table
Time aspects affecting paint
• Shelf Life
• Pot Life
• Induction Time
• Drying Times (Surface dry, hard dry, fully cured)
• Re-coating Interval
• Humidity (Actual, maximum and relative humidity)
• Temperature (Air, substrate and process temperatures)
• Dew Point
ISO 12944 - Paints and varnishes - Corrosion protection of steel structures by protective paint systems
ISO 12944-1 : General introduction
ISO 12944-2 : Classification of environments (corrosivity)
ISO 12944-5 : Protective paint systems